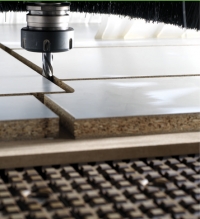
Wraz z nowym modelem centrum obróbczego Rover A G FT włoska firma Biesse wprowadziła niezwykle wydajny system rozkroju płyty na formatki do produkcji frontów czy elementów korpusów meblowych. – To rewolucyjny krok w rozwoju technologii nestingu i optymalizacji produkcji mebli kuchennych – zapewnia Claudio Tornati, prezes zarządu TEKNIKA, wyłączny przedstawiciel Biesse w Polsce.
Sama idea nestingu nie jest niczym nowym. Producenci mebli, jeszcze zanim sprzężono maszyny stolarskie z "mózgiem" komputera, starali się tak rozłożyć formatki na arkuszu płyty, by jak najbardziej zaoszczędzić materiał. Dziś zadanie to jest znacznie prostsze dzięki maszynom sterowanym numerycznie, które wyposażone w odpowiednie oprogramowanie i zastosowanym algorytmom, dokonują optymalizacji rozkroju. Ich wyższość polega na możliwości pobierania dodatkowych informacji z różnych baz danych np. złożonych zamówień od klientów czy stanów magazynowych zakładu. Co zatem jeszcze można ulepszyć w tego typu technologii, prócz wprowadzania coraz to bardziej wydajnych procesorów komputerowych, zdolnych przeliczać coraz większe ilości danych i przekształcać je w zadania dla obrabiarki?
![]() |
Niezwykle wydajny system rozkroju płyty na formatki do produkcji frontów czy elementów korpusów meblowych , w jaki wyposażono nowy model centrum obróbczego Rover A G FT, to rewolucyjny krok w rozwoju technologii nestingu. Fot. TEKNIKA |
Po pierwsze wydajność i elastyczność
Za wzrostem mocy obliczeniowych procesora musi pójść wydajność samej maszyny. Głowica wiertarska z 17 wrzecionami zamontowanymi w nowym centrum Rover A G FT pracuje z maksymalną prędkością obrotową nawet 6000 rpm i jest bezstopniowo regulowana przez falownik. Szybką zmianę narzędzi, bez konieczności zatrzymania maszyny, umożliwia magazynek rewolwerowy z 16 zasobnikami, zamontowany na jednostce obróbczej osi X. Elektrowrzeciona wyposażone są w uchwyty typu ISO 30 lub HSK F 63. To wszystko czyni tę maszynę nie tylko centrum obróbczym do rozkroju, lecz także nawiercania otworów czy frezowania krawędzi. Stąd prócz formatowania, nawierceń pod łączniki czy gniazda elementów korpusu mebla kuchennego wykonanego z płyt wiórowych, maszyna może również frezować, grawerować czy zaoblać kształty frontów meblowych z MDF czy sklejki.
Po drugie gabaryty i mocowanie
Producenci płyt drewnopochodnych oferują coraz to większe formaty zarówno w przypadku płyt wiórowych, MDF, jak i sklejek. Udana konstrukcja stabilnego belkowego stołu roboczego Rover A G TF o długości 3765 mm pozwala na ułożenie dużych formatów płyt i elastyczne rozłożenie elementów mocujących. Mocowanie odbywa się na zasadzie bloków podciśnieniowych – jest to najnowocześniejsze na świecie rozwiązanie, które wyróżnia się spośród dotychczas znanych rozwiązań bardzo wysoką odpornością na siły poziome działające podczas obróbki. Przyssawki charakteryzują się specjalną, przemyślaną konstrukcją, dzięki której nawet wielokrotne uszkodzenie gumy uszczelniającej nie wymaga jej natychmiastowej wymiany. Bloki podciśnieniowe wyposażone są również w zawory krańcowe pozwalające na pozostawienie przyssawek, które nie będą wykorzystane podczas cyklu obróbczego. Najważniejsze jest jednak to, że elementy mogą być swobodnie rozmieszczane bez konieczności stosowania dodatkowych połączeń.
Po trzecie podawanie i odbiór
Dzięki systemom e-commerce, jak choćby sklepy internetowe, znacznie zwiększyła się szybkość przekazywania danych od zamawiającego kuchnie salonu meblowego do fabryki. Oczekuje się także, że czas realizacji zamówienia będzie coraz krótszy. Usprawnieniom musi ulec zatem nie tylko czas obróbki elementów, lecz także ich logistyka a to wiąże się z koniecznością automatyzacji procesów podawania surowca i odbioru, a następnie kompletowania elementów. Rover A G TF jest tak skonstruowany, że operacje załadunku i rozładunku odbywają się w tym samym czasie. Jest to moment, w którym maszyna skupia się już na obróbce nowych elementów, a w tym czasie operator może bezpiecznie wyjąć gotowe elementy ze stacji rozładunkowej. Podawanie płyt odbywa się automatycznie przy pomocy przenośników podciśnieniowych, co gwarantuje nie tylko bezpieczeństwo, ale także brak uszkodzeń płyty podczas załadunku. Jeszcze w trakcie, gdy maszyna obrabia pozostałe płyty, gotowe elementy są automatycznie etykietowane kodem kreskowym.
![]() |
Konstrukcja stabilnego belkowego stołu roboczego Rover A G TF o długości 3765 mm pozwala na ułożenie dużych formatów płyt i elastyczne rozłożenie elementów mocujących. Fot. TEKNIKA |
Po czwarte sterowanie i kontrola
Problemem wielu centrów obróbczych jest to, że ich producenci nie nadążają za zmianami w zakresie rozwoju systemów operacyjnych, co stanowi poważny problem w procesach integracji maszyn z komputerami projektantów mebli czy działu rozwoju produktu. W przypadku maszyn Biesie, takich jak Rover, mamy do czynienia z autorskim systemem Biesseworks, niezwykle zaawansowanym i wybiegającym w przyszłość, jednak bazującym na popularnym systemie operacyjnym Windows. Do tego graficzny interfejs tego oprogramowania jest niezwykle przyjazny i intuicyjny dla operatora maszyny. Łatwo integruje się z programami do projektowania, umożliwiając import plików typu CAD z rozszerzeniem DXF i CID3. Biesseworks ma także bardziej zaawansowane możliwości w zakresie symulacji 3D toru narzędzia, orientacyjnego obliczenia czasu obróbki danego zadania itp. Zaletą tego systemu jest jego modułowość i możliwość rozbudowy np. o system BiesseNest, który umożliwia przekształcenie w zadanie optymalizacji rozkroju nawet najbardziej skomplikowanych kształtów. Z kolei BiesseCabinet to świetny moduł dedykowany producentom szaf, który w prosty sposób pomaga zarządzać rozmieszczeniem wyposażenia garderoby: np. wieszaków, półek, szuflad czy drzwi.