Cezary Pacholik
Uszczelnienia stosowane w elementach pneumatycznych są jednym z ich najważniejszych komponentów. Od nich zależy pewność pracy oraz czas eksploatacji produktu, a w konsekwencji satysfakcja użytkownika oraz producenta. Celem niniejszego artykułu jest przybliżenie podstawowych rozwiązań uszczelnień technicznych, zadań przed nimi stawianych oraz materiałów stosowanych do ich produkcji. Z uwagi na złożoność zagadnienia omówione zostaną wiadomości podstawowe. Pełne zgłębienie tematu wymaga specjalistycznej wiedzy teoretycznej oraz wieloletniego doświadczenia.
Uszczelnienia statyczne
Zadaniem stawianym przed uszczelnieniami statycznymi jest uszczelnienie połączenia pomiędzy dwoma, wzajemnie nieruchomymi powierzchniami.
W przypadku podzespołów wykonanych ze stosunkowo elastycznego tworzywa sztucznego (żywica acetalowa) stosuje się specjalne ukształtowanie u wylotu z gwintu co eliminuje konieczność stosowania jakichkolwiek, dodatkowych uszczelniaczy. Dla elementów mniejszych rozmiarów oraz do połączeń gwintowych stosuje się uszczelnienia ciekłe np. kleje anaerobowo-stykowe.
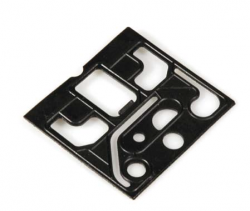
dla powierzchni płaskich
Uszczelnienia dynamiczne
Uszczelnienia dynamiczne zapewniają szczelność połączenia pomiędzy podzespołami poruszającymi się względem siebie. Rozróżnia się uszczelnienia do ruchu obrotowego oraz liniowego; z uwagi na charakter pracy elementów pneumatycznych (dla siłowników: uszczelnienie tłoka oraz tulei, tłoczyska z pokrywą przednią, oraz zaworów rozdzielających uszczelnienie zaworów względem korpusu) w dalszej części zostaną omówione uszczelnienia dla ruchu liniowego.
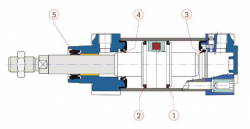
Przekrój typowego
siłownika pneumatycznego
Uszczelnienia typu O-ring
W odróżnieniu od uszczelnień statycznych, w aplikacjach dynamicznych stosuje się przekrój eliptyczny lub „S”.
Odmienny od kołowego przekrój zapewnia wyższą elastyczność promieniową oraz dużą powierzchnię kontaktu pomiędzy uszczelnieniem a płaszczyzną. Elastyczność promieniowa jest niezbędna do kompensowania odchyłek wymiarowych na całym odcinku pracy.
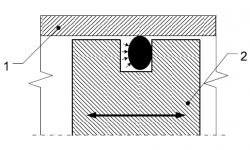
Uszczelnienia wargowe
Budowa uszczelnienia wargowego zapewnia szeroki zakres dopuszczalnych odchyłek wymiarowych uszczelnianej powierzchni oraz kompensację własnego zużycia. Wyższe ciśnienie pracy zapewnia wyższy stopień szczelności połączenia. Z uwagi na powyższe zalety jest to najczęściej stosowany rodzaj uszczelnienia w siłownikach pneumatycznych. Na rysunku 3 przedstawiono uszczelnienia wargowe w typowym siłowniku pneumatycznym: (1) oraz (2) uszczelnienia wargowe tłoka, (5) uszczelnienie dwuwargowe tłoczyska – jedna warga uszczelniająca, druga – zgarniająca, (3) oraz (4) uszczelnienia jednokierunkowe amortyzacji pneumatycznej – zapewniają szczelność w jednym kierunku oraz swobodny przepływ w drugim.
Uszczelnienia metal-metal
Jest to rodzaj uszczelnienia labiryntowego opierającego się na bardzo małej (ściśle określonej) wartości luzu pomiędzywspółpracującymi powierzchniami. Stosowane w przypadku pracy w środowiskach zapylonych oraz w aplikacjach wymagających najniższych wartości współczynnika tarcia. Rozwiązanie charakteryzuje się ciągłym upustem powietrza do atmosfery, który ulega zwiększeniu wraz z zużyciem elementów.
Podstawowe materiały stosowane do produkcji uszczelnień komponentów pneumatycznych:
Guma butadienowo-nitrylowa - NBR - najczęściej stosowany materiał do produkcji uszczelnień.
Główne cechy:
- wysoka kompatybilność z olejami, smarami oraz węglowodorami;
- elastyczność, pamięć elastyczności;
- zakres temperatur roboczych – 10 °C do + 90 °C Stosowanie specjalnych domieszek umożliwia obniżenie dolnego zakresu temperatury roboczej do – 50 °C.
Poliuretan: PU lub AU – uszczelnienia z poliuretanu charakteryzują się bardzo wysoką odpornością na ścieranie, zapewniając długi okres eksploatacji produktów.
Główne cechy:
- bardzo wysoka elastyczność;
- pamięć kształtu: powrót do pierwotnego kształtu nawet po długiem czasie odkształcenia;
- wysoka odporność na ścieranie;
- możliwość stosowania przy dużych prędkościach liniowych;
- brak kompatybilności z wieloma gatunkami oleju,włączając oleje sprężarkowe;
- podatność na hydrolizę przy obecności wody;
- podatność na kruszenie przy wysokich temperaturach;
- zakres temperatur roboczych – 20 °C do + 80 °C.
Guma fluorowa - FKM/FPM – stosowana w aplikacjach wymagających wyższej odporności chemicznej lub przy wysokich wartościach temperatury otoczenia.
Główne cechy:
- bardzo wysoka odporność chemiczna, kompatybilnośćz wieloma substancjami;
- niższa elastyczność (w stosunku do poliuretanu);
- niższa ścieralność (w stosunku do poliuretanu);
- zakres temperatur roboczych – 10 °C do + 150 °C.
Guma nitrylowa uwodorniona - HNBR – materiał chemicznie bardzo zbliżony do NBR.
Główne cechy:
- wyższa ścieralność (w stosunku do NBR);
- zakres temperatur roboczych – 30 °C do + 150 °C.
Guma etylenowo – propylenowa - EPDM – stosowana do wysokich temperatur oraz gorącej wody i pary wodnej.
- brak kompatybilności z wieloma gatunkami oleju orazwęglowodorami;
- zakres temperatur roboczych – 30 °C do + 150 °C.
Na rysunku 4 przedstawiono porównanie podstawowych parametrów uszczelnień gdzie najlepszy materiał przyjmuje wartość 100, dla danej kategorii służąc jako odniesienie.
Rys. 4 Wykres porównawczy elastomerów
Tribologia
Nawet doskonałe uszczelnienie ulegnie bardzo szybkiemu zużyciu bez odpowiedniego czynnika smarnego.Trwałoś ć uszczelnienia oraz produktu zależą w znacznej mierze od typu zastosowanego smaru.
W odróżnieniu od produktów starszej generacji, używanie smarownic jest nie tylko niekonieczne ale wręcz niezalecane. Bardzo często, wskutek usunięcia smaru stałego przez mgłę olejową ze smarownicy oraz niesystematycznego jej uzupełniania dochodzi do tarcia suchego wewnątrz elementów pneumatycznych i w konsekwencji do zakłóceń w pracy, oraz ich przyspieszonego zużycia.
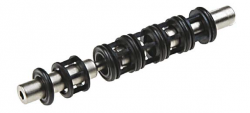
Obecnie, właściwie wszyscy producenci komponentów pneumatycznych posiadają w ofercie siłowniki oraz zawory ze smarem stałym, przewidzianym na całą żywotność lub bardzo długi okres eksploatacji produktu. Stosowane smary stałe, dzięki wieloletnim badaniom oraz doświadczeniom są bardzo zaawansowanym produktem, dlatego też należy używać wyłącznie zalecanych smarów.
Ostatnim czynnikiem mającym wpływ na poprawną oraz długą pracę uszczelnienia jest chropowatość oraz twardość powierzchni współpracującej z uszczelnieniem – czynnik równie istotny jak dobór smaru oraz materiału i przekroju uszczelnienia. Bardzo często stosuje się dodatkową obróbkę powierzchniową oraz pokrywanie wybranych powierzchni dodatkowymi powłokami o określonych parametrach fizykochemicznych. Jako przykład, na rysunku 5 przedstawiono suwak zaworu poddany chemicznemu niklowaniu i polerowaniu.
Mamy nadzieję że podane informacje okażą się pomocne dla osób poszukujących właściwych rozwiązań.